Product Spotlight | Lifting Magnets
Product Spotlight | Lifting Magnets
Lifting magnets, also known as magnetic lifters, or magnetic lifting systems, are a versatile piece of rigging equipment that can be used in a variety of applications ranging from lifting small metal pipes or scraps to large heavy metal blocks.
If your business deals with a lot of heavy ferrous metals (generall meaning, containing iron) it may be a good idea to invest in a lifting magnet! Most general permanent lifting magnets have a working load limit (WLL) ranging from 500 to 3,000 pounds, with some electromagnets reaching a WLL of 11,000 pounds – This offers an easy, efficient and cost-effective way to lift an array of metal loads.
Lifting magnets are commonly used in steel mills, scrap yards, loading docks, warehouses, foundries, shipyards, coil and pipe distributors, and other users of applicable steel products.
Types of Lifting Magnets
There are two basic types of lifting magnets – permanent magnets and electromagnets.
Permanent Magnets
Permanent magnets are exactly what you’d think- They’re permanent! What that means is that these magnets use materials that are permanently (or naturally) magnetized to establish the magnetic field. These are called ferromagnetic materials and are usually iron, nickel, or alloys that are made or rare-earth metals.
Fun fact: The main way that permanent magnets are created is by heating a ferromagnetic material to a key high temperature – Specific to each kind of metal. This is similar to the natural process that takes place inside the Earth which is what creates materials that are naturally magnetized.
The majority of permanent lifting magnets can be “turned on” and “turned off” by way of a lever. These magnets generally have two parallel poles which give the magnet a deep penetrating magnetic field for rougher flat surfaces and round pipe or shaft material. When both pole’s fields are lined up, with North to North and South to South, the magnetic field is activated, but when you pull the lever those fields are reversed which will cause the lifting magnet to let go of the load.
Electromagnets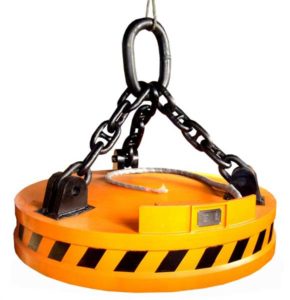
Electromagnets, unlike permanent magnets, rely on electricity to charge the magnet and hold the load to the face of the magnet. This takes place by the use of an energized electrical coil wrapped around a steel core creating a magnetic field. This, of course, means the lifting magnetic depends on a constant power source, which also means a lack of access to power or a power failure can mean the equipment can’t be used.
A safety hazard to keep in mind when using electromagnets in the fact that If the electric current is interrupted, any load being hoisted would be released and dropped. Some electromagnets feature a battery that will protect against accidental loss of power or power outages.
Fully battery-powered magnets are also available which use a self-contained gel cell-type batteries. Battery-powered magnets can be moved from hoist to hoist, offering generous lifting capacity without an external power connection with only a need for periodic recharging.
The Advantages of Lifting Magnets
The three main advantages of lifting magnets are their ability to lift materials without needing to cause surface damage, their cost-saving benefits, and their level of efficiency.
And this is how…
Damage-Free Lifting: Like lifting clamps, lifting magnets provide a way to transport materials without needing to cause surface damage to the load, such as needing to drill a hole to place an eyebolt. They can also minimize the potential of causing scratches, holes, or dents in the material if the magnets are used properly!
Cost-Effective: Since you are able to perform lifts without causing any damage to the load, it results in a more cost-effective lift since there’s no need to then fill and re-finish said damage. It also can be a more costly lift, simply because of the time saved in its efficiency…
Efficiency: Beyond lifting loads with no damage, lifting clamps are also often used to pick materials that may not be accessible enough to properly attach other rigging equipment. For example, if you have a crate of tightly packed materials come in, you may be able to use a lifting magnet to access one part from the top and lift it out quickly and easily! If this crate was say, filled with pipes stacked horizontally, using a strap or chain to lift a single pipe would require one end of the part to be manually lifted in order to pass the strap or chain underneath – Which would at the very least take much more time – If not being totally impossible, impractical or unsafe.
5 Things to Keep in Mind When Using Lifting Magnets
Every type of lifting equipment has downfalls you need to keep in mind to ensure you’re rigging safe – And lifting magnets are no exception to that rule!
Above all, it’s imperative to have proper training on the correct use of ANY rigging equipment you come in contact with on the job. Once you have that base of knowledge, these are a few things you’ll want to be reminding yourself when using a lifting magnet.
1. Air Gaps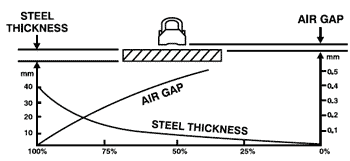
An air gap between the magnet and the load’s surface can reduce it’s holding performance. Magnetic lines of force pass easily through ferrous metals, but not air – Therefore anything that creates space or an air gap between the magnet and the lifted object will have a negative impact on the lifting capacity of the magnet. To get the best holding performance, air gaps must be kept to a minimum. You can determine the possibility of air gaps by looking at the profile of the load and its surface. Keep an eye out for things like thick paint, dust, chips, paper or packaging, rust, moisture or textured surface finishing which can all cause air gaps.
2. Magnet Contact to Surface
Always ensure the entire magnet surface is making contact with the load during the lift. The lifting capacity of the magnet will be reduced in direct proportion to any amount of lack of contact with the material surface.
3. Material Being Lifted
Not all ferrous metals are made alike – Some contain non-magnetic materials that have a negative impact on the magnetic conductance. Heat treatments that affect the structure of the metal can also reduce the lifting capacity.
The lifting force percentage of various materials:
- St37 (0,1-0,3% C) = 100% lifting force
- Non-alloy steel (0,4-0,5% C) = 90% lifting force
- Cast steel = 90% lifting force
- Alloy steel F-522 = 80% – 90% lifting force
- AISI430 (magnetic stainless steel) = 50% lifting force
- Cast iron = 45% – 60% lifting force
- F-522 tempered (60 HRC) = 40% – 50% lifting force
- AISI304 (stainless steel/nickel) = 0% – 10% lifting force
- Brass, aluminium, copper, etc. = 0% lifting force
4. Bending of the Load
If you’re lifting material with a single magnet such as a thin sheet, or something much wider then it is long, be conscious of the load bending and possibly, ‘peeling off’ the magnet. To combat this, thin sheets should be lifted with multiple magnets evenly distributed over the entire surface, and the magnet contact surface should always be in line with the lifted load, not perpendicular to its length.
5. Thickness of the Load
Think of magnetism as lines flowing from one material to the next, sticking them together – like a bunch of invisible nails. Have you ever tried to hang a photo on the wall with a nail and it fell right back out because the drywall wasn’t thick enough for the nail to properly be secured? Magnetism works very similar to that. Only if the load is sufficiently thick is it possible to utilize the magnet’s full capacity. Once this point is reached, a greater material thickness will not result in any additional lifting capacity. If the material you’re trying to lift is too thin, you won’t be able to use your lifting magnets full capacity.
Hercules SLR makes lifting magnets for a wide range of applications using permanent, electro-permanent, battery-powered, and electromagnetic technologies. Lifting Magnets are versatile, compact, easy to operate and can be used on flat and round material ranging from 0 to 11,000lbs. Our larger lifting magnets are designed for applications such as handling billets, bundles, bar stock, slabs, plates, structural, long bar stock, rail, hot material, coils, pipe rebar, radioactive material, slag, and more.
——————————————————————————————————————————————
The Hercules Group of Companies encompasses a wide portfolio of products and services across 7 diverse companies.