A Brief History of Elevator Wire Ropes
A Brief History of Elevator Wire Ropes
The humble hoisting rope occupies a unique place in the history of vertical transportation. A simple hemp rope lies at the center of one of the best-known elevator stories — Elisha Graves Otis’ demonstration of his Improved Safety Device at the 1854 Crystal Palace in New York City.
Currently, a sophisticated carbon nanotube “rope” is the primary innovation driving the conceptual (and possibly literal) development of the proposed “space elevator”. However, the wire rope retains pride-of-place in elevator history as the longest-serving suspension means. It is the subject of numerous 19th-century articles that questioned its safety, and has been featured in countless contemporary books, movies and TV programs that predicate disaster on its failure. Today, we look at the introduction of wire elevator ropes in the 19th century and its development into the 20th century.
The invention of wire rope more-or-less paralleled the invention of the passenger elevator, and, by the 1870s, wire rope had become the rope of choice for elevator use. Since they were new, both the elevator and wire rope faced similar challenges regarding safety concerns. The older hemp hoisting rope had a long history of use, and its strengths and weaknesses were well known. However, a rope made of wire was an entirely different matter. This difference was effectively summarized in the June 22, 1878, issue of American Architect and Building News, which included a brief article on elevator ropes. The article expressed the primary concern in its opening sentence:
“The sudden introduction in our large cities of elevators, most of which are hung by wire ropes, has led people to wonder what will happen when they have had a year’s wear, and why there should not, after a while, be a breaking of ropes, and consequent accidents all over the country.”
The key concern centered on the endurance of elevator wire rope and its reaction to constant and repeated bending as it passed around winding drums and over sheaves. One of the aforementioned article’s key assumptions was that “everybody knows, at least, that reiterated bending weakens wire, whether it be by granulation or by the constant extension of its fibers.” The challenge was, in spite of “knowing” that this action occurred, there was no easy way to judge when a rope was no longer safe for use.
The ICS author also addressed rope replacement, noting that “particular attention must be given to the fastenings.” The chief recommendation was to “carefully reproduce the joint as it was originally made” by the elevator manufacturer. A typical shackle used by Otis Elevator is described below in figure 1.
Figure 1: “Otis Elevator Co. Shackle,” ICS Reference Library (1902). Pictured right
It consists of a split rod, the two legs A, A of which are bulged out and provided with noses at the ends. A collar B straddles the legs and eventually abuts against the noses. The rope is brought through the collar, bent over a thimble C, and passed back again through the collar, after which the free end is fastened by wrapping with wire. The wrapped end of the sections that address elevator wire ropes serves as a reminder that different elevator systems required different types of rope:
- Chapter 1: Standard Methods and Facilities for Testing Wire Ropes
- Chapter 2: Materials Composing Wire Rope and Their Properties
- Chapter 3: Standard Types of Wire Rope Construction
- Chapter 4: Variety of Uses of Wire Rope
- Chapter 5: Mechanical Theory of Wire Rope
- Chapter 6: Practical Hints and Suggestions
- Chapter 7: Instructions on Ordering Wire Rope
- Chapter 8: Typical Applications of Wire Rope in Practice
“When ordering rope for elevators, state whether hoisting, counterweight, or hand or valve or safety rope is wanted, also whether right or left lay is desired. The ropes used for these purposes are different and are not interchangeable.”
The diversity of elevator wire ropes was reflected in the design of American Steel & Wire’s standard hoisting rope, which was produced in six grades or strengths: Iron, Mild Steel, Crucible Cast Steel, Extra Strong Crucible Cast Steel, Plow Steel and Monitor Plow Steel. The company’s standard iron rope was primarily designed for use on drum machines and was “used for elevator hoisting where the strength is sufficient” (Figure 2). It was also described as “almost universally employed for counterweight ropes, except on traction elevators.” Their Mild Steel Elevator Hoisting Rope was designed “especially for traction elevators in tall buildings where, on account of [the] usual quick starting and stopping, a stronger and lighter rope is required.” Shipper or control ropes (also called tiller or hand ropes) differed from standard ropes in that they were composed of six strands of 42 wires each, which were wrapped around seven hemp cores (Figure 3).
In addition to providing detailed information on a wide variety of wire ropes, the catalog included schematic drawings that illustrated their proper application. These included 17 elevator-related drawings that depicted direct-, side- and horizontal-plunger hydraulic elevators; geared and traction electric elevators; and electric and belt-driven worm-geared elevators. The drawings’ emphasis on the application of wire ropes makes them a unique resource. Two versions of direct-plunger elevators were depicted — one with a shipper rope and one with an in-car controller — and the presence of two elevation drawings for each system permits a thorough understanding of these elevators (Figure 4). The same level of detail was provided for side-plunger hydraulic elevators (manufactured by Otis) and horizontal-plunger hydraulic systems (Figures 5 and 6).
Figure 6: “Horizontal Hydraulic Elevator,” American Wire Rope: Catalog & Handbook, American Steel & Wire (1913)
Figure 6
The electric elevator drawings are of particular interest, because, in 1913, they represented the newest systems on the market. The electric drum machine featured an interesting array of sheaves for the car and counterweight ropes, while the worm-gear machine employed a winding drum located near the midpoint of the shaft (Figures 7 and 8). The traction elevator drawing effectively illustrated its inherent simplicity and the potential of this new design (Figure 9).
The variety of elevator types illustrated in American Steel & Wire’s catalog represented the diversity of elevator systems prevalent in the early 20th century, as well as the importance of wire rope to their operation. Part Two of this article will follow this story through the 1930s, which encompasses the continued development of the traction elevator and the writing of the first elevator safety codes.
Figure 7: “Electric Drum Machine,” American Wire Rope: Catalog & Handbook, American Steel & Wire (1913).
Figure 7
Figure 8: “Worm Gear Electric Elevator,” American Wire Rope: Catalog & Handbook, American Steel & Wire (1913).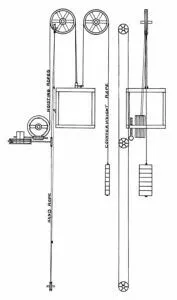
Figure 8
Figure 9: “Traction Elevator,” American Wire Rope: Catalog & Handbook, American Steel & Wire (1913).
Figure 9
——————————————————————————————————————————————
The Hercules Group of Companies encompasses a wide portfolio of products and services across 7 diverse companies.